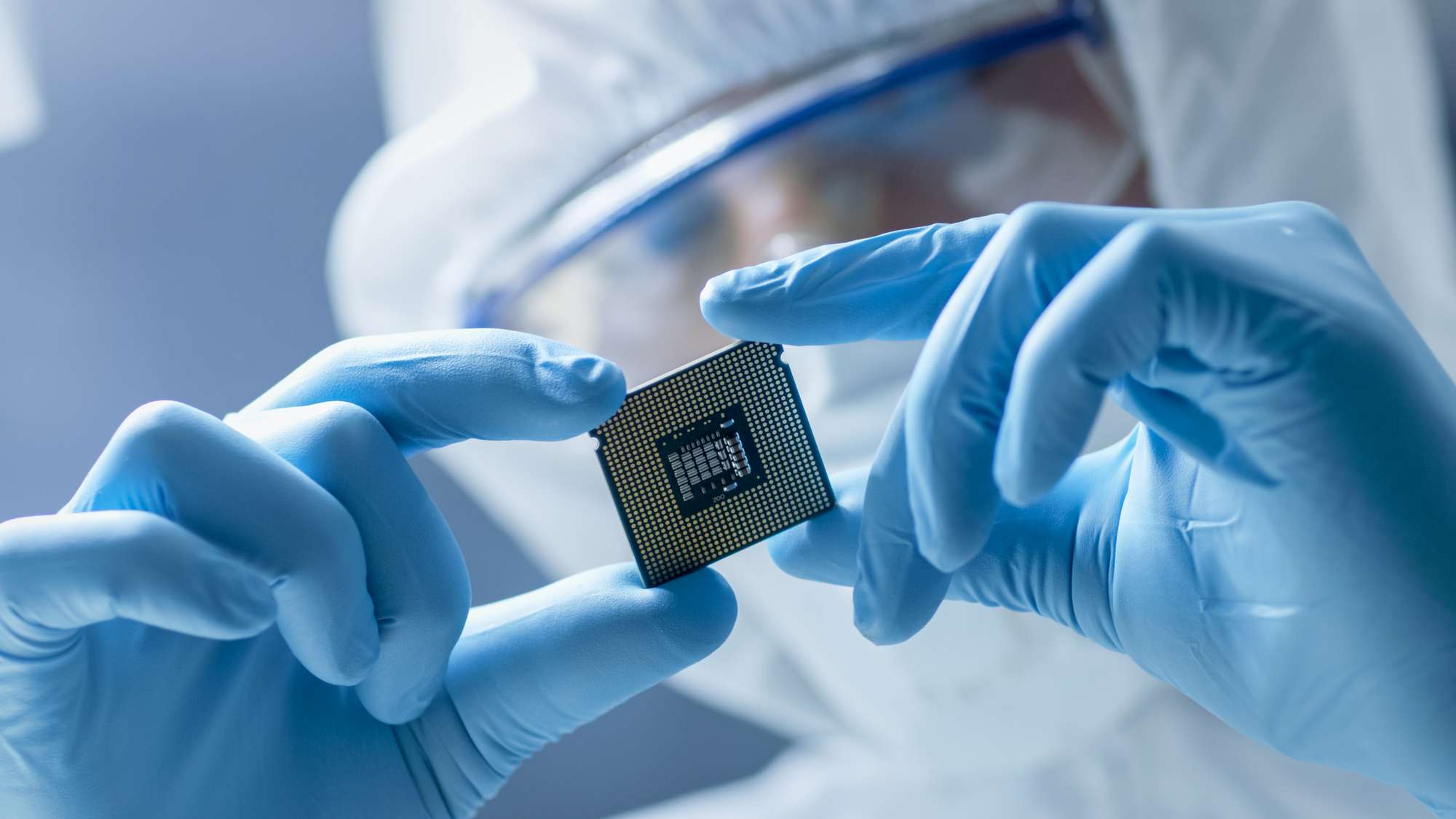
Blog / An Update on the Microchip Shortage
Experts are divided on when the microchip shortage will end, but they all agree it’s not over yet.
Although there’s no arguing that the defining news story of the last few years has been the COVID-19 pandemic, a close runner-up has been the development and recovery of the silicon microchip shortage that has stalled production on everything from cars to computers to cameras. Whether it’s from rising prices or long delivery delays, any and every manufacturer that uses a chip in its products has been impacted.
Of course, as with all things in the news cycle, hot headlines about the topic quickly became backup stories. However, just because it’s not making headlines anymore doesn’t mean the shortage has gone away.
How did we get here?
It’s easy to blame supply-chain breaks and shortages on the pandemic and associated lockdowns, but that’s only part of the story. Geopolitics got it all started, and a string of bad luck made things worse.
The problem started in the summer of 2019, well before COVID emerged, when the US began restricting the export of certain technologies to China. Not happy being blacklisted, Chinese manufacturers began refusing orders or delivery to American clients. This was nowhere near enough to kickstart the shortage, but it set the stage and left western manufacturers with little no excess inventory to prop up any shortcomings should they arise.
And arise they did. As COVID began it’s spread across the world, manufacturers began shutting down. The automotive industry, now hugely reliant on semiconductors, reduced orders and intentionally slowed their own production anticipating demand to drop. Meanwhile, with people locked up at home, electronic device and IoT product sales started to boom. When automotive demand recovered faster than expected, it was too late. What semiconductors manufacturers had stockpiled prior to lockdowns had already been snapped up by other sectors, and when weeks of shutdowns dragged on into months there was virtually no production to fill the void. Given this situation a shortage was, in hindsight, inevitable.
So when will it end?
Well, that’s the multibillion-dollar question. There’s been some significant movement on the part of governments and private industry to address supply-chain issues and other bottlenecks, including investment in new domestic (American) production facilities. Canada’s tech sector is particularly interested in developing Canadian onshore manufacturing, recently creating the Canadian Semiconductor Council which envisions a robust and world-renowned fabrication sector in the great white north by 2050.
However, the CSC’s long-term plans won’t help with short term supply. Moreover, it’s been difficult to get fabrication back online, hindered by plain old bad luck. A headline-grabbing, electrical-grid destroying cold snap put a freeze on Samsung, Infineon, and NXP Semiconductors’ manufacturing in Texas. This was followed a month later by factory fire in a Japanese plant (responsible for 1 in 3 vehicle chips) where almost two dozen fabrication machines were destroyed. Intermittent shutdowns and new waves of COVID variants are further hampering efforts to get chip production back online.
As a result, no one can really say with any degree of certainty how long the shortage will last. No doubt it’s already easing, but expert opinions range from the middle of 2022 to sometime in late 2023 before chip manufacturing can satisfy the pent-up demand. The truth is, even a year later, no one truly knows when the shortage will end.
How do we deal with the microchip shortage until then?
To be honest, the glib but mostly correct answer is you don’t. We’re talking about a worldwide microchip shortage that developed from an unprecedented confluence of events that no one was prepared for. In situations such as these, there’s not much that can be done. However, there are a few things SMBs and other organizations can do minimize the impact on their operations.
First, make sure your technology assessments and requirements for the near future are accurate. It’s not impossible to obtain business-grade equipment if you’ve already committed to an upgrade or implementation, but you may want to re-evaluate your requirements for the next 18 to 24 months and plan to give lots of lead time (perhaps as much as six months) between ordering and delivery.
Second, make sure you know and understand your equipment’s end-of-support and end-of-life dates. We came down pretty hard on letting your technology age out recently, and we stand by that advice. Nevertheless, given the current situation (and for the foreseeable future), it would be smart for organizations to maximize their equipment’s usefulness and lifespan rather than investing while prices are artificially high. That might include opting for extended manufacturer’s warranty on critical equipment, upgrading user devices with additional RAM or drive space to add capacity, or offloading internal server-intensive applications and data to a Cloud service. A perfect example is migrating to Microsoft’s Exchange Online Email system and retiring your internal email server, which could be re-deployed for other purposes in your organization.
Semiconductor microchips are the backbone of our computerized world, making their shortage particularly painful. Unfortunately, except for taking extra care to ensure your equipment’s value and lifespan are maximized, there’s not a lot that can be done to avoid the sting. When equipment purchases are unavoidable, accurate estimations of requirements and an MSP that understands how to source business grade equipment are your best friends, so if you’d like help sourcing or extending the lifetime of your aging technology, contact TRINUS today!
Sincerely,
The TRINUS Team
trinustech.com